Images from a dekra vt1000
Imagine uncovering the hidden issues within industrial machinery before they escalate into costly repairs. The images from a dekra vt1000 pitting images revolutionize the approach to inspection, allowing professionals to detect early signs of corrosion. This guide explores what these images reveal and their role in safeguarding industrial assets.
Introduction to DEKRA VT1000 Pitting Images
Assessing corrosion in industrial environments can be challenging. However, the images from a dekra vt1000 stands out as a leading tool for visual inspections, specifically designed to identify and analyze pitting corrosion—a prevalent concern across various industrial sectors.
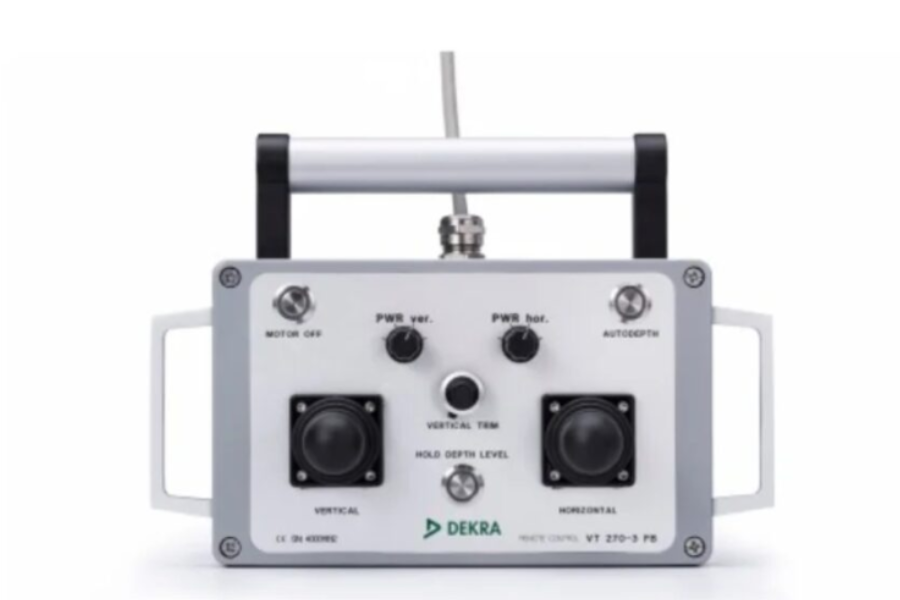
What is DEKRA VT1000?
The images from a dekra vt1000 is a state-of-the-art visual inspection system that empowers industry professionals to accurately assess the severity of pitting corrosion. Utilizing high-resolution imaging and sophisticated analytics, it provides detailed insights into the condition of metal surfaces, enabling early detection and intervention.
Importance of Visual Inspection
Conducting visual inspections is crucial in the realm of corrosion management. Experts utilize the images from a dekra vt1000 to meticulously examine metal surfaces for signs of pitting corrosion. This technology enhances the clarity, consistency, and reliability of visual analysis, guiding companies in making informed decisions regarding asset maintenance and management.
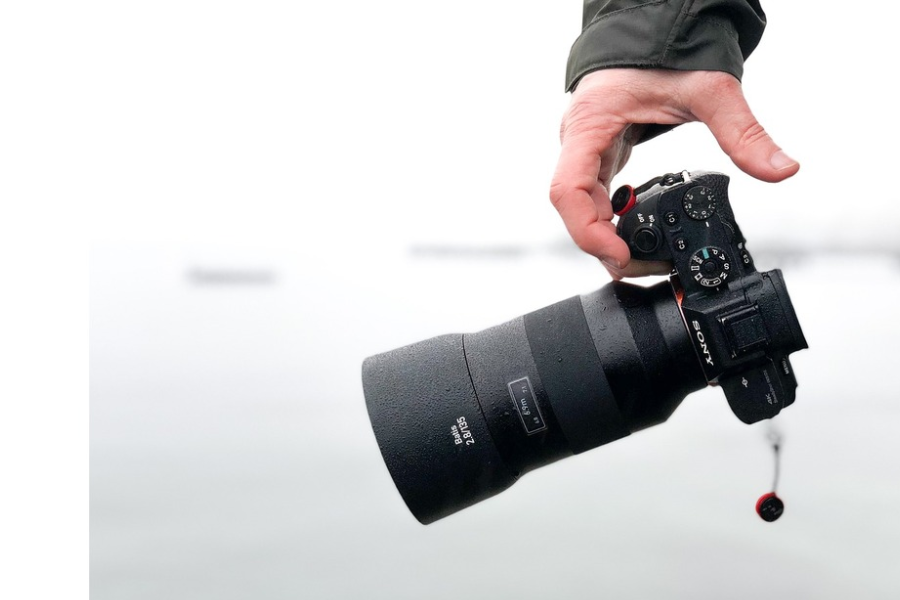
By leveraging the images from a dekra vt1000 for corrosion assessments, organizations can gain a profound understanding of their equipment’s health, prioritize maintenance efforts, and extend the lifespan of their assets, thereby reinforcing the significance of visual inspections in ensuring industrial safety and efficiency.
Understanding Pitting Corrosion
Pitting corrosion presents a serious risk, resulting in localized defects on metal surfaces. These small, often undetectable holes can expand and lead to significant equipment failure if not addressed.
Key Factors Contributing to Pitting Corrosion:
- Metallurgical Composition: Certain metals, like stainless steel, are inherently more susceptible to pitting.
- Environmental Conditions: Corrosive environments, such as those with high salt content, accelerate pitting corrosion.
- Mechanical Stress: Stressors on metal can increase vulnerability to pitting.
- Surface Impurities: Contaminants or defects on metal surfaces can initiate pitting.
Understanding the mechanisms behind pitting corrosion is essential for its prevention, ensuring the integrity of critical industrial equipment.
Types of Corrosion
Type of Corrosion | Characteristics | Causes |
Pitting Corrosion | Small, localized depressions on the surface | Metallurgy, environmental factors, mechanical stress |
Uniform Corrosion | Gradual and even loss of material | Corrosive environments and lack of protective coatings |
Galvanic Corrosion | Accelerated corrosion due to dissimilar metals contact | Contact of different metals in the presence of an electrolyte |
DEKRA VT1000 Pitting Images Gallery
Visual inspection plays a pivotal role in identifying and assessing corrosion damage. The DEKRA VT1000 provides a comprehensive collection of pitting images, enabling a better understanding of varying corrosion levels. This gallery aids in recognizing light, moderate, and severe pitting corrosion, facilitating accurate evaluations of asset conditions.
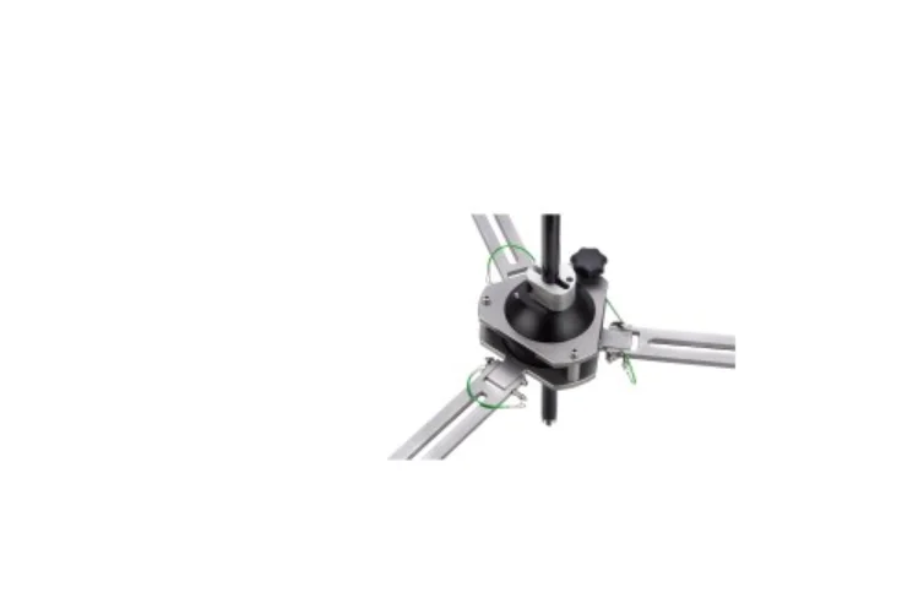
Types of Pitting
- Light Pitting: Characterized by shallow, small depressions. While minor, these can indicate future issues if left unchecked.
- Moderate Pitting: Displays deeper, more prominent pits that suggest escalating corrosion. These require timely attention to prevent material weakening.
- Severe Pitting: Represents significant damage with deep, interconnected pits that jeopardize structural integrity. Immediate intervention is necessary to avert major failures.
Interpreting DEKRA VT1000 Pitting Images
Proper interpretation of DEKRA VT1000 pitting images is critical for assessing corrosion damage. Understanding evaluation criteria and acceptance levels allows for informed decision-making regarding asset maintenance.
Evaluation Criteria
The assessment of DEKRA VT1000 images involves specific criteria, focusing on:
- Pit Size: Measuring the dimensions of each pit against established standards.
- Distribution: Analyzing the proximity and spread of pits.
- Surface Area Impacted: Evaluating the extent of the surface affected by pitting.
Acceptance Levels
The DEKRA VT1000 images are compared against corrosion acceptance standards that determine the condition of the equipment:
Corrosion Severity | Acceptance Level |
Light Pitting | Acceptable for continued operation |
Moderate Pitting | Requires monitoring and further evaluation |
Severe Pitting | Unacceptable; immediate action required |
Through an understanding of these interpretations, professionals can make strategic decisions to maintain asset integrity.
Preventive Measures for Pitting Corrosion
Mitigating pitting corrosion is vital for preserving the performance and lifespan of industrial equipment. Implementing design strategies and material choices can significantly reduce corrosion risks.
Design Considerations
When developing systems, consider the following principles to minimize pitting corrosion:
- Reduce crevices and sharp edges where corrosive agents may collect.
- Ensure proper drainage and ventilation to avoid stagnant conditions.
- Use protective coatings or linings that offer a barrier against corrosive elements.
- Design for ease of access to facilitate regular inspections.
Material Selection
Choosing the right materials is essential for enhancing corrosion resistance. Consider these factors:
Material | Resistance to Pitting | Advantages | Disadvantages |
Stainless Steel | High | Durable, corrosion-resistant | Higher cost than carbon steel |
Titanium | Very High | Lightweight, excellent corrosion resistance | Expensive compared to stainless steel |
Nickel-Based Alloys | High | High-temperature tolerance, corrosion-resistant | Costly compared to stainless steel |
DEKRA VT1000 Certification Process
Obtaining DEKRA VT1000 certification signifies a commitment to excellence in corrosion inspection. This certification validates professionals’ capabilities in accurately assessing asset conditions.
The training process is rigorous, encompassing the principles of visual inspection, including the identification and evaluation of pitting corrosion. Candidates are required to master both theoretical knowledge and practical applications.
Certification Requirements
To achieve certification, candidates must successfully complete examinations covering:
- DEKRA VT1000 standards and protocols
- Corrosion mechanisms and assessment methods
- Interpretation of visual inspection data
- Documentation and reporting standards
Maintaining certification involves ongoing education and adherence to DEKRA’s guidelines, ensuring professionals remain current in their field.
Best Practices for Visual Inspection
Conducting thorough visual inspections is crucial for effective corrosion management. Utilizing the DEKRA VT1000 requires adherence to best practices to ensure accurate results.
Preparation and Equipment
Before initiating a visual inspection, it’s essential to gather the appropriate tools and establish a safe work environment. Prepare the DEKRA VT1000 inspection system for high-quality imaging, and ensure personal protective equipment (PPE) is worn, including safety goggles, gloves, and appropriate clothing.
Inspection Techniques
During the inspection, prioritize a detailed and methodical evaluation of surfaces. Incorporate a combination of visual inspection best practices and corrosion assessment methodologies:
- Scrutinize surfaces for signs of pitting or localized corrosion.
- Utilize adequate lighting and magnification to enhance visibility of small pits.
- Capture high-resolution images for analysis and documentation.
- Measure pit depth and size to assess severity accurately.
- Compare observations to industry standards for precise evaluations.
By adhering to these best practices, visual inspections utilizing DEKRA VT1000 Pitting Images will yield valuable insights, aiding in proactive corrosion management.
Case Studies: DEKRA VT1000 in Action
The practical application of DEKRA VT1000 has proven invaluable in various industrial contexts, empowering professionals to address pitting corrosion with confidence. Here are a couple of notable examples:
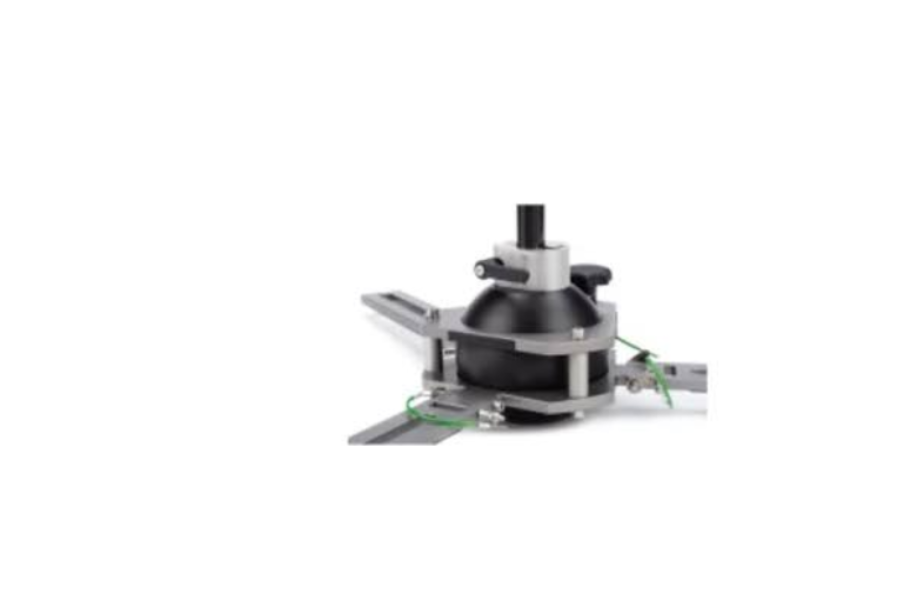
- A prominent oil and gas corporation employed DEKRA VT1000 Pitting Images for their pipeline infrastructure. The detailed visual data allowed their team to detect early signs of pitting corrosion, enabling targeted maintenance efforts that prevented costly shutdowns and ensured operational safety.
- In the automotive manufacturing sector, a leading supplier utilized DEKRA VT1000 Pitting Images to assess their production machinery. The high-resolution images facilitated informed decisions regarding component replacements, extending equipment lifespan and optimizing maintenance schedules.
FACTS
1. Metallurgical Composition
Different metals exhibit varying susceptibility to pitting corrosion based on their intrinsic properties. For example:
- Stainless Steel: While generally resistant, it can experience pitting in chloride-rich environments.
- Aluminum Alloys: These can suffer from pitting when exposed to alkaline solutions.
2. Environmental Conditions
The environment plays a significant role in the onset of pitting corrosion:
- Chloride Presence: High chloride concentrations, often found in seawater, accelerate corrosion rates.
- Temperature: Elevated temperatures can enhance the aggressiveness of corrosive agents.
3. Mechanical Stress
Mechanical factors can increase the likelihood of pitting corrosion:
- Stress Concentrations: Areas subjected to tensile stress are more prone to localized corrosion.
- Fatigue Loading: Repeated stress cycles can lead to the initiation of pits.
4. Surface Impurities
Impurities on metal surfaces can act as initiation points for pitting corrosion:
- Contaminants: Dirt, grease, or foreign materials can create localized corrosion sites.
- Defects: Surface imperfections or inclusions can promote the development of pits
Frequently Asked Questions (FAQs)
Q: What is pitting corrosion, and why is it a concern?
A: Pitting corrosion is a localized form of corrosion that leads to the formation of small holes (pits) in metal surfaces. It is a concern because it can compromise the structural integrity of equipment, potentially leading to catastrophic failures and costly repairs.
Q: How does the DEKRA VT1000 assist in detecting pitting corrosion?
A: The DEKRA VT1000 uses high-resolution imaging technology to capture detailed images of metal surfaces. These images help professionals identify and assess the severity of pitting corrosion, enabling early intervention and maintenance.
Q: What are the benefits of obtaining DEKRA VT1000 certification?
A: Certification validates professionals’ expertise in corrosion inspection and management. It demonstrates a commitment to best practices and ongoing education in corrosion detection and assessment techniques.
Q: What preventive measures can be taken to reduce pitting corrosion?
A: Preventive measures include selecting appropriate materials, designing systems to minimize crevices, ensuring proper drainage, and applying protective coatings to shield surfaces from corrosive elements.
Q: How often should visual inspections be conducted using the DEKRA VT1000?
A: The frequency of inspections depends on the specific industry, equipment usage, and environmental conditions. Regular inspections should be part of a comprehensive maintenance plan to ensure asset integrity.
Conclusion
The DEKRA VT1000 pitting images are indispensable tools for assessing and managing pitting corrosion in industrial environments. This guide has explored the importance of visual inspections, the mechanics of pitting corrosion, and the capabilities of the DEKRA VT1000 system.
By effectively utilizing these images, industry professionals can enhance their understanding of corrosion severity, implement timely maintenance measures, and ultimately extend the lifespan of their assets. The integration of advanced visual inspection technologies like the DEKRA VT1000 not only safeguards equipment but also contributes to improved operational safety and efficiency across various industrial sectors. As organizations continue to prioritize asset integrity, the significance of such inspection systems will undoubtedly grow, reinforcing the need for ongoing education and adherence to best practices in corrosion management.
Read More: Evolve To Future